Реактор за Полярным кругом
Работы по проектированию Билибинской атомной электростанции начались на основании Постановления Совета Министров СССР от 8 октября 1965 года. Постановление предусматривало строительство Билибинской АЭС установленной электрической мощностью четырех энергоблоков 48 МВт и выработкой тепла до 100 Гкал/ч для энергоснабжения быстро развивавшегося Билибинского горнопромышленного узла на базе крупных месторождений золота. Научное руководство по созданию атомной энергоустановки было возложено на Физико-энергетический институт, Генеральным проектировщиком станции назначено Уральское отделение института «Теплоэлектропроект».
Имея опыт эксплуатации реактора АМ и АМБ-100, специалисты ФЭИ сделали выбор в пользу водографитового реактора с трубчатыми твэлами, отказавшись от идеи ядерного перегрева пара. Это вызвало недовольство руководства НИИ-8 (НИКИЭТ), которое отказалось браться за проект, и Главным конструктором реакторной установки становится техническое бюро «Энергоблок» Минэнергомаша.
К новым реакторам предъявлялись повышенные требования к надежности, ведь создание специализированной ремонтной базы на Севере существенно удорожало проект. Имеющиеся серийные насосы главного циркуляционного контура этим не отличались, поэтому проектировщикам поставили обязательное условие работы реакторной установки при естественной циркуляции воды в главном контуре. Это было внове для канальных водографитовых установок, таких аналогов в мире еще не существовало. В связи с этим в проектируемом аппарате был применен ряд новых технических решений: многопетлевая конструкция контура естественной циркуляции, коллекторная схема отвода пароводяной смеси от технологических каналов в барабан-сепаратор, струйное смесительное устройство питательной воды, измененная конструкция технологического канала.
Новый реактор получил название ЭГП-6 — Энергетический Гетерогенный Петлевой реактор с 6-ю петлями циркуляции теплоносителя.
Тепловая мощность реактора ЭГП-6 была принята 65 МВт, электрическая — 12 МВт. Первые расчетные оценки гидравлических характеристик контура естественной циркуляции показали, что при длине трубчатого твэла 3 м суммарная высота контура естественной циркуляции должна составлять 26 м.
В обоснование выбранных проектных решений в ФЭИ был создан полномасштабный стенд, содержащих два макета ТВС с шестью твэлами каждый, на котором проверялись гидродинамические характеристики установки. Испытания на стенде подтвердили возможность работы энергоустановки в режиме естественной циркуляции теплоносителя.
Реакторная установка получила шесть циркуляционных петель, замкнутых на барабан-сепаратор. Компоновка контура естественной циркуляции имела два уровня оборудования: нижний — реактор, верхний — барабан-сепаратор. Оба узла связаны шестью групповыми опускными трубопроводами, по которым к реактору подается вода, и шестью групповыми подъемными трубопроводами, по которым от реактора отводится пароводяная смесь.
Групповая петля контура естественной циркуляции реакторной установки включала в себя систему параллельных трактов тепловыделяющих сборок (30-33 шт. и 52-54 шт.). В свою очередь каждая из тепловыделяющих сборок (ТВС) представляла собой систему из шести параллельных трактов трубчатых твэлов с проходным внутренним диаметром 10,8 мм.
Технологические каналы реактора размещаются в графитовой кладке. Кладка реактора имеет цилиндрическую форму диаметром 6 м и высотой 5,25 м. Она сложена из отдельных графитовых и в верхней части чугунных блоков квадратного сечения. Центральная часть графитовой кладки диаметром 4,1 м и высотой 3 м, представляющая собой активную зону реактора, состоит из 333 вертикальных колонн с отверстиями диаметром 88,6 мм по всей высоте, в которых размещаются 273 рабочих канала и 60 каналов СУЗ. Кладка реактора смонтирована на стальной плите и размещена в стальном герметичном кожухе, заполненном азотом. Верхняя часть кладки толщиной 1 метр является одним из элементов биологической защиты реактора.
Паропроизводительность реакторной установки составляла 90 т/час при давлении 6,37 МПа и температуре питательной воды 104 °С.
Для Билибинской АЭС была спроектирована уникальная система охлаждения, специально приспособленная для полярных условий. Конденсаторы турбин станции охлаждаются водой, которая затем охлаждается в воздушно-радиаторных охладителях, использующих находящийся в избытке холодный воздух. Охлаждение происходит за счет принудительной прокачки воздуха через радиаторы длиною 6 м и шириною 2,5 м вентиляторами диаметром 3,5 метров. Летом дополнительно применяется система пиковых охладителей. Вода теплосети, предназначенная для обогрева жилых зданий, нагревается предварительно в основных подогревателях, питаемых паром из регулируемых и нерегулируемых отборов турбины.
5 марта 1967 года Билибинская АЭС объявлена Всесоюзной ударной комсомольской стройкой, и уже 21 июня на стройку прибыла первая группа молодежи из 120 человек. В конце декабря 1967 года на месте котлована главного корпуса прогремел первый взрыв.
Монтажные работы по сооружению станции начались в 1969 году, и вел их тогда участок треста «Дальэнергомонтаж». В начале 1971 года его сменил Билибинский монтажный участок треста «Востокэнергомонтаж», специалисты которого имели опыт монтажа оборудования крупнейших ГРЭС, а также участвовали в сооружении ядерных реакторов военного назначения в Красноярске-26. Они продолжили монтаж каркаса главного корпуса и радиаторных охладителей, трубопроводов и оборудования 1-го энергоблока.
В середине июня 1971 года начала работать пусковая котельная — первый пусковой объект. А в ноябре 1973 года паром, который давала пусковая котельная, был произведен пробный пуск турбины первого энергоблока с испытательным прокручиванием ее до 3000 оборотов в минуту и продувкой всех технологических паропроводов станции.
Физический пуск ядерного реактора энергоблока № 1 Билибинской АЭС проходил в период с 10 по 31 декабря 1973 года. При пуске первого реактора проводились детальные исследования физических характеристик активной зоны, чтобы внести, если потребуется, изменения в загрузку последующих реакторов. Поэтому при пуске определялись параметры критических сборок, а именно, минимальные критические загрузки, эффективность технологических каналов и каналов СУЗ, распределение потоков нейтронов по радиусу и высоте сборок. После проведения экспериментов на сборках реактор был полностью загружен топливными каналами, заполненными водой. Всего в реактор были загружены 217 топливных каналов с 3 % обогащением урана и 56 каналов с обогащением 3,3 %, последние были установлены в периферийные ячейки активной зоны.
Измерения во время пуска показали, что основные физические характеристики реактора ЭГП-6 соответствуют расчетным. А уже 12 января 1974 года первый энергоблок Билибинской АЭС дал первый промышленный ток в сеть Чаун-Билибинского энергоузла. Выход на проектную мощность энергоблока состоялся в середине 1974 года.
В дальнейшем атомные реакторы вводились в строй как на конвейере. 30 декабря 1974 года был введен в эксплуатацию энергоблок № 2, еще через год — 22 декабря — к нему присоединился и энергоблок № 3. Последний, четвертый энергоблок Билибинской АЭС встал в строй действующих 27 декабря 1976 года, после чего атомная станция вышла на свою проектную мощность в 48 мегаватт.
Станция спроектирована по блочному принципу, в соответствии с которым все четыре реактора расположены в одном реакторном отделении. Здание АЭС сооружено на монолитных железобетонных плитах с предварительным оттаиванием грунта под фундамент. Наружные стены реакторного зала изготовлены из алюминиевых панелей. В связи с отсутствием бетонных стен при перегрузке топливных каналов используется специальный защитный контейнер. С его помощью топливные каналы выгружаются в хранилище, находящееся в реакторном зале.
Пар из реактора поступает на теплофикационную турбоустановку электрической мощностью 12 МВт, изготовленную в ЧССР и работающую на насыщенном паре при давлении 5,9 МПа.
Каждый энергоблок может работать в базовом режиме и режиме переменных нагрузок. Это стало возможным благодаря особой конструкции активной зоны. Во-первых, для твэлов была подобрана дисперсионная топливная композиция на основе магния с высокой теплопроводностью. Во-вторых, созданы «щадящие» условия работы твэла — умеренная его теплонапряженность. В третьих, слабое изменение расхода естественной циркуляции в контуре реакторной установки. Эти факторы позволяли менять мощность реактора в диапазоне мощности 50-100 % за 3 часа.
Но не все гладко. На этапе опытно-промышленной эксплуатации энергоблока № 2 на мощности 20 % был выявлен брак при монтаже расходомерных вставок в групповых петлях, что приводило к недостоверным показаниям расхода воды. Для перемонтажа требовался останов реактора, что привело бы к срыву плановых сроков пуска. Руководство станции приняло решение не останавливать реактор, и произвести перемонтаж после этапа опытно-промышленной эксплуатации. В результате энергоблок № 2 был пущен в установленные сроки.
Физический пуск энергоблока № 4 должен был состояться в сентябре 1976 года, однако в процессе пуска в активной зоне были обнаружены области повышенного поглощения нейтронов, что существенно увеличило критическую массу реактора. Оказалось, что Московский электродный завод поставил на станцию бракованные графитовые блоки с высоким содержанием бора. Монтажникам пришлось перекладывать графитовую кладку, что на квартал отложило пуск блока.
Энергоблоки Билибинской АЭС демонстрировали высокие технико-экономические показатели. До 1990-х годов средний КИУМ станции достигал 80 %, а коэффициент готовности составлял 90-92 %.
Перегрузка реакторов ЭГП-6 осуществляется при помощи разгрузочно-загрузочной машины. Перегрузка производится при остановленном и расхоложенном реакторе и, как правило, приурочивалась к проведению профилактических и ремонтных работ. Число перегружаемых сборок зависело от длительности планируемого межперегрузочного интервала. Как правило, замены 80 технологических каналов хватало на год работы реактора.
При перегрузке каналов необходимо было произвести расстыковку каналов с подводящими и отводящими трубопроводами. Доступ к головкам каналов, расположенных под верхней плитой реактора, производился через верхнее перекрытие, разделяющее надреакторное помещение и центральный зал. Перекрытие представляло собой два вращающихся защитных барабана — большой и внутри него — малый, оси которых расположены эксцентрично. В малом вращающемся перекрытии выполнена выемная пробка, после извлечения которой производились операции по отстыковке.
Реакторы ЭГП-6 за все время эксплуатации демонстрировали высокий уровень надежности. За все время эксплуатации была зарегистрирована только одна аварийная ситуация «мокрого» типа — разрушение одного твэла в реакторе блока № 2. Кроме того, была зафиксирована повышенная утечка азота из газового контура и протечки бака биологической защиты блока № 1. Устранение этих дефектов велось с использованием сложного робототехнического оборудования. За период 1979-1985 гг. число аварийных остановов реакторов ЭГП-6 составило менее одного в год. Анализ времени простоя энергоблоков показал, что по вине реактора простой составил только 1,3 % от общего времени, а из-за турбоустановок — 33,4 %.
Проектный срок эксплуатации каждого из энергоблоков заканчивался 11 января 2004 года, 31 декабря 2004 года, 31 декабря 2005 года и 31 декабря 2006 года соответственно. При этом реакторные установки относились к первому поколению, и приведение их в соответствие с действующими нормами безопасности было весьма затруднено. Тем не менее, после проведенной модернизации срок эксплуатации каждого энергоблока был продлен на 15 лет.
23 января 2019 года Федеральная служба по экологическому, технологическому и атомному надзору выдала концерну «Росэнергоатом» лицензию на эксплуатацию в режиме без генерации энергоблока № 1 Билибинской АЭС, остановленного для вывода из эксплуатации. Лицензия выдана на 15 лет (до 2034 г.).
Это один из этапов жизненного цикла блока АЭС, между его работой на мощности и полным выводом из эксплуатации. На данном этапе Росэнергоатом, как эксплуатирующая организация, должен будет осуществить как перевод блока АЭС в ядерно-безопасное состояние, так и разработку соответствующего комплекта документов, обосновывающего ядерную и радиационную безопасность при выводе блока из эксплуатации. Он потребуется для получения лицензии Ростехнадзора на следующий этап — вывод блока № 1 из эксплуатации.
Фотогалерея3

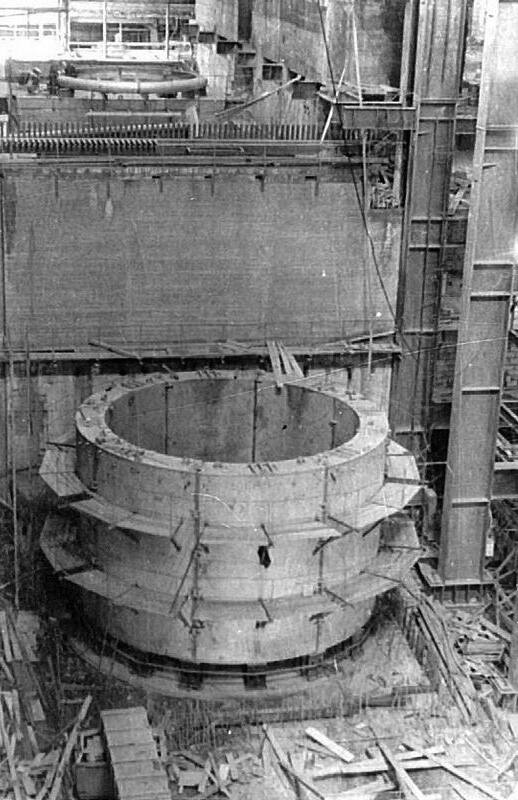
